Production Process
Welcome!
This page offers a rare glimpse into facets of the saxphone-making craft at Yanagisawa.
- 1. Body Fabrication
- 2. Press Operations
- 3. Post and Key Fitting
- 4. Surface Finishing
- 5. Final Assembly and Inspection
- 6. Cleaning, Packing, and Shipment
- 7. Mouthpieces
1. Body Fabrication
Sheets of brass and other alloys are cut and welded to form the tubing for the bell, bow, body, and neck; tone holes are drilled and drawn from the body tubing; and the bodies are then inspected and passed on to the next stage.
1. Materials
Rolls of metal sheet stock are sorted by brass, bronze, and silver alloy and utilized in different combinations depending on the saxophone model being made. Each roll is about 30 meters long.
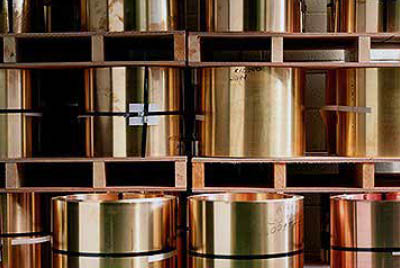
2. Welding the main body tube
The connecting edges are lined up and seamlessly welded together with a 1000 C torch.
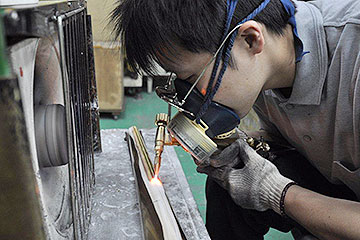
3. Hammering
Any bumps or pits that remain after the welding stage are hammered and smoothed out to hide the joint seam.
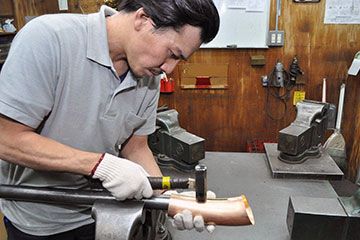
4. Body molding
A metal mold is used to shape the body . An inserted tool forces the body through a slightly smaller-diameter hole in a metal plate. The hole in the plate is adjusted for changes in body taper.
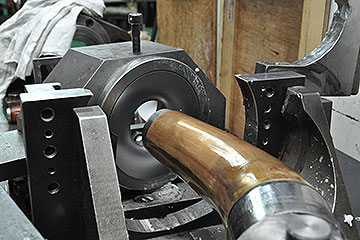
5. Shaping the bell
Sections of the bell that cannot be shaped by machine are spun on a lathe and shaped with a variety of handheld spatula tools.
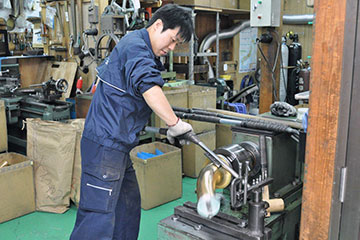
6. Tone hole drilling
Tone hole locations are drilled into the shaped and polished body components after they are placed in a special die.
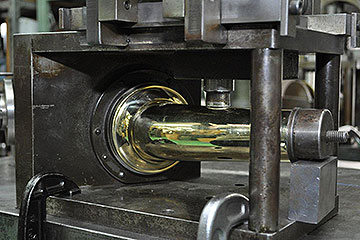
7. Tone hole drawing
When the handle is turned, a round piece is pulled through to form and draw out the tone hole from the wall of the body tubing. Special care is the rule when fabricating tone holes because they have the most significant influence on the saxophone's scale.
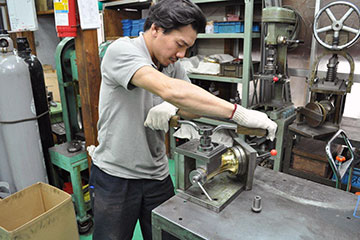
2. Press Operations
All key parts are cut, punched, shaped, and welded together using an assortment of die and press tools.
On average, as many as 10 different steps are involved in the production of each finished part.
1. Press forming
Sax key parts and certain body components are punched out on press machinery. Over 10 variations in thickness are used for such punched-out parts.
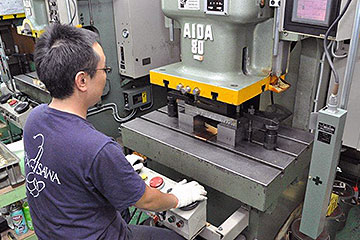
2. Press-punched parts
Parts initially punched out with press machinery also go through fabrication stages that involve drilling, bending, and shaping operations.
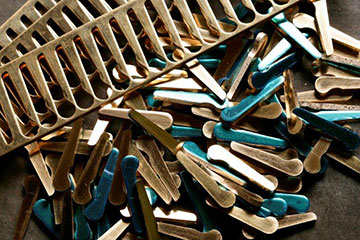
3. Parts fabrication
Many parts created with press machinery eventually reach their final shape after further processing with a wide array of cutting tools.
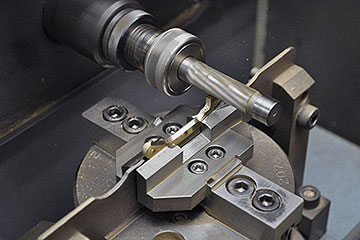
4. Press dies
An assortment of press dies used to make various parts. Multiple dies are used in the production of each individual part. The factory uses over 2,000 dies in all.
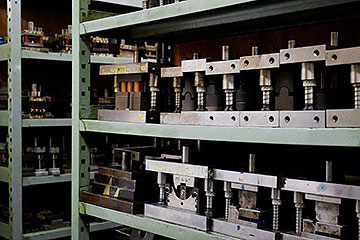
5. Post fabrication
Sax posts of different sizes and shapes are cut to precision dimensions on CNC lathes.
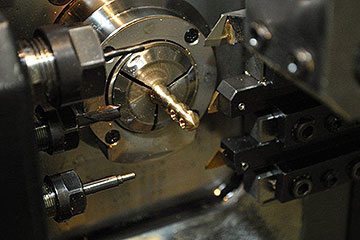
6. Soldering
Over 120 different types of parts are created by silver-soldering key cups and other components to sax hinge rods and hinge tubing.
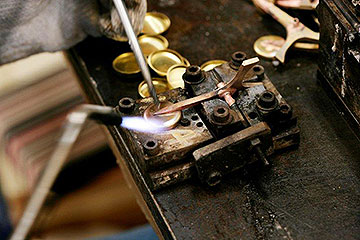
7. Parts stock
Our materials stockroom has inventory in approx. 400 different types of finished saxophone parts.
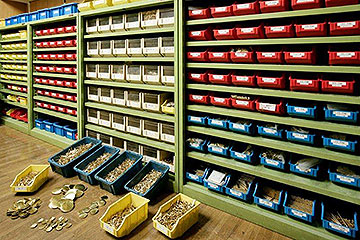
3. Post and Key Fitting
This stage comprises attaching the posts to the body and fitting the keys.
Extreme care is exercised during the key-fitting work to ensure that the final assembly stage flows more smoothly.
1. Attaching the posts
Post assemblies are soldered to the body with a 400 C torch.
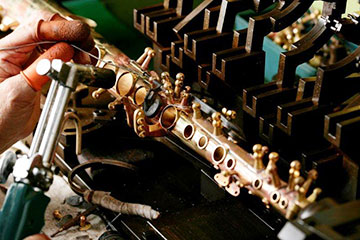
2. Key fitting(1)
The bell and bow are soldered together, giving the sax its basic form.
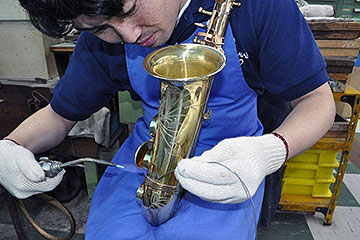
3. Key fitting (2)
Preliminary key fitting is performed to enhance the precision fit of the key mechanism in the final assembly stage. The sax is also checked for silver-solder residues and flaws in the key mechanism.
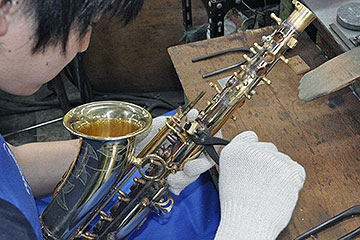
4. Engraving
Each saxophone is hand-engraved by a devoted artisan.
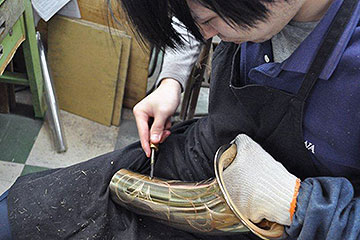
4. Surface Finishing
This stage comprises dipping each sax body in a chemical solution to remove excess solder residues from the post fitting process and then buffing and spray-lacquering it along with its finished set of custom-fit keys.
1. Buffing the keys
The body and all keys are buffed and polished prior to lacquering.
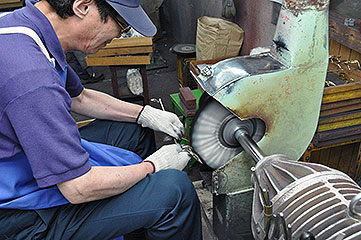
2. Buffing the body
The body is polished in several steps with each pass utilizing a softer abrasive compound or buffing wheel.
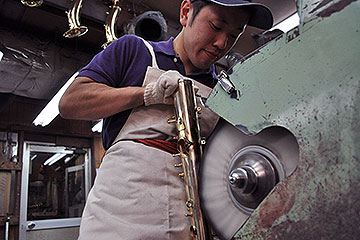
3. Ultrasonic cleaning
Prior to lacquering, everything is given an ultrasonic bath. This cleaning process completely removes all oils and buffing compound residues.
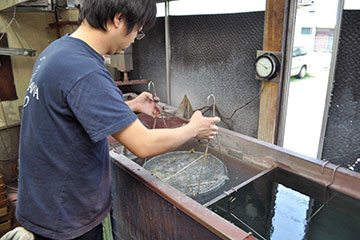
4. Lacquering
All parts are sprayed with a lacquer coat and then placed in an oven to heat-cure the lacquer.

5. Final Assembly and Inspection
With their sparkling new finish, the sax body and its keys now look completely different. Once the pads, corks, and felts are installed, it is time for final assembly. Extra caution is essential now because anything that is scratched or otherwise blemished during these steps will not be suitable for sale as a finished product.
1. Installing the pads and cork materials
Pads and cork materials are installed on already-lacquered keys. We use three types of pad adhesive that vary by melting temperature. Also, to minimize the need for post-assembly adjustments, we use a composite pressed cork that maintains its shape and firmness.
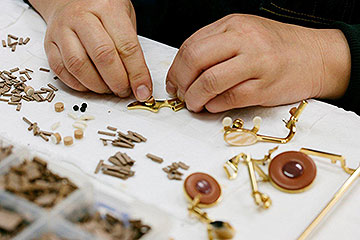
2. Assembly (1)
During assembly we apply a tape film to protect each instrument from scratches. Assembly proceeds with installation of the right-hand keys followed by the left-hand keys and then the side keys.
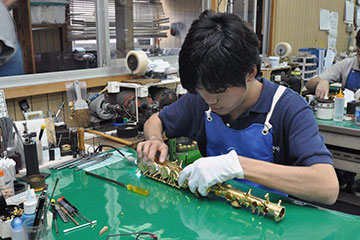
3. Assembly (2)
Using a leak light, each pad seat is checked for air leaks and adjusted as necessary.
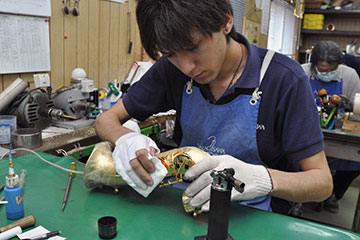
4. Assembly (3)
The assembly process is complete when the bell is attached to the instrument and the low-note bell keys controlled by the left-hand little finger are finally installed and regulated.
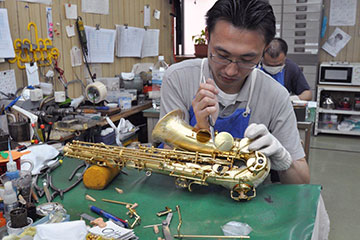
5. Inspection
The instrument-making process concludes with a final, meticulous inspection of each fully assembled instrument. This inspection includes balancing the keys, tensioning the springs, and precision-fitting the neck.
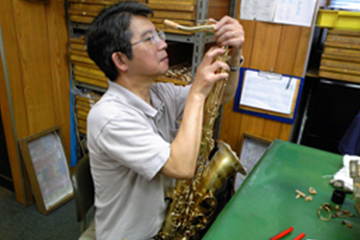
6. Cleaning, Packing, and Shipment
1. Cleaning
Following final inspection, the protective tape is removed and the sax is polished with a cleaning cloth to remove any fingerprints and smudges from the preceding work stages. Additionally, it will be checked over one last time for scratches or other blemishes.
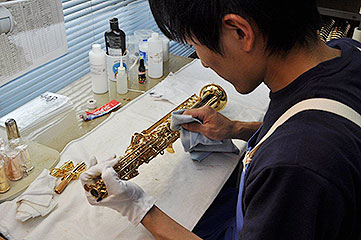
2. Packing (1)
Once cleaned and polished, the sax is carefully placed inside its case.
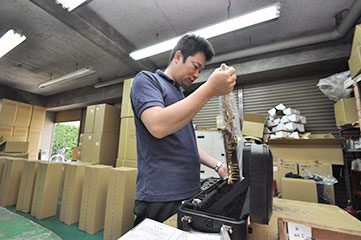
3. Packing (2)
Each and every cased instrument is then packed in a sturdy cardboard shipping container.
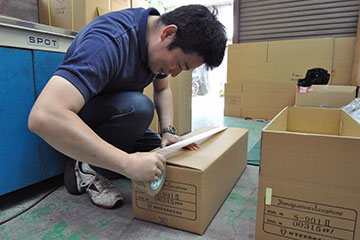
4. Shipment
Packed instruments are loaded onto a truck at the warehouse and shipped to domestic distributors or to port facilities for export. Yanagisawa saxophones are supplied to the domestic Japanese market and exported to more than 20 national markets around the globe.
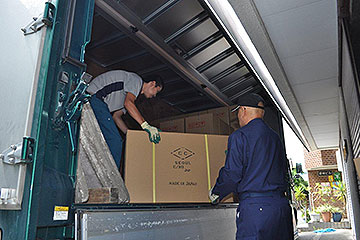
7. Mouthpieces
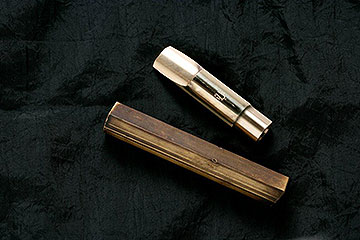
On the bottom is a sample of the material used to make a metal mouthpiece.
On top is a partially machined mouthpiece blank.
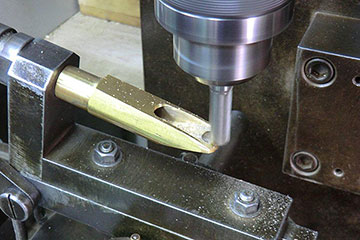
Preliminary machining of the baffle area.
(In later stages the baffle will be further shaped and refined with files and abrasive cloth.)
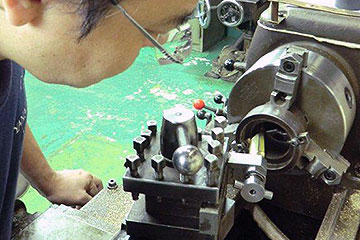
Machining the inlay area for the ebonite bite-plate insert.
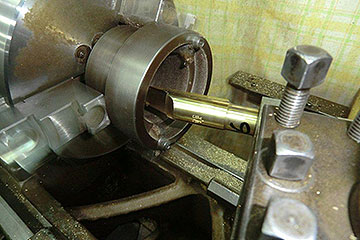
A close-up view.
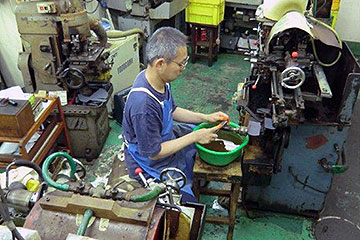
The ebonite machining process.
Machinery shown here is used to cut and shape the ebonite blank.Machining marks are removed with wet sandpaper.
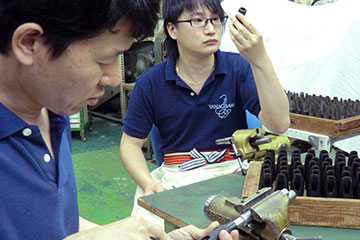
Filing the baffle and finishing with abrasive cloth.
Afterward, the outer surface is polished, the baffle and table areas are perfected, and the mouthpiece is ready to go.
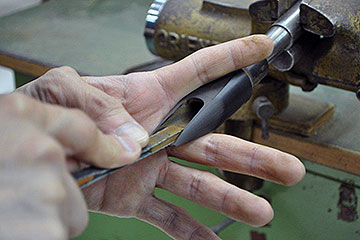
A close-up view.
Although many other processes are involved in the manufacture of Yanagisawa saxophones, we hope this tour was enlightening.
Currently our factory engages about 100 employees in the entire instrument-making process.
Saxophones are actually delicate instruments.
Few people probably know this but the body metal is typically only around 0.7-0.8 mm thick. The instrument can of course easily be dented or bent if knocked against something or even if allowed to fall over while inside its case.
Many players that use gig bags or soft cases end up with dented horns before they are aware of the risks.
The pads as well as certain other parts are wear items. Unless the saxophone is properly swabbed and cleaned after playing, the pads will quickly begin to show wear.
We recommend that you have your saxophone inspected and adjusted on a regular basis or at least once every three to four months.
This will ensure that it is always in top performing condition.
At Yanagisawa, we build each and every saxophone with the utmost devotion and attention to detail. We urge that players also show care for their horns.
Rest assured yours will reward you with a better playing experience in return.